Technical Solutions

GUIDANCE TECHNOLOGY
For our AGV/AMR, we always use the most appropriate methods of guidance technology, based on the given needs of the project. There are areas where magnetic tape still has its place, mainly for moving parts between machines. But for transporting the part from the machine to the warehouse, SLAM navigation is fully applied, which uses LiDAR or a camera for guidance. Another variant is the use of GPS, which is used for outdoor applications. If necessary, GPS navigation can be made more precise by using stationary base stations. We can also use a combination of different types of navigation for applications that require it. It is always necessary to correctly evaluate the installation options, the accuracy of navigation, the division of spaces, the width of transport routes, the movement of people and other transport techniques in space, moving obstacles, changing basic orientation points and the financial costs of individual types of navigation.
Currently, the most common guidance methods are:
- Magnetic tape is stuck to the floor and RFID tags (chips) are embedded in the floor next to the magnetic tape
For narrow transport aisles and fixed routes, magnetic tape guidance is the optimal solution with regard to price, performance, required transport capacity and safety.
- SLAM navigation (Simultaneous Localization and Mapping)
Based on the data obtained from the laser distance sensor, gyroscope, speedometer and accelerometer, the algorithm creates a map of the environment and safely plans a driving route.
- cheap
- quick and easy fix
- resistant to environmental influences
- visible AGV travel path = reduced risk of collision
- inflexible (must be re-glued when changing route)
- risk of damage
- does not allow automatic obstacle avoidance
- without marking the route on the floor
- accurate +/- 1 cm
- suitable for complex and rugged routes
- SW flexible
- can act as a virtual tape
- option of automatic bypassing of obstacles
- combination with other types of navigation
- higher acquisition costs
- if the corridor is not structured (columns, other protruding parts), it is necessary to install a reflector every 8 metres

CUSTOM BATTERY LIFEPO4
To be able to offer AGV/AMR in various dimensions, including very low platforms, we started the production of our own batteries. We are now able to offer LiFePo4 – type batteries not only for our vehicles but also for your applications. We offer 24 V and 48 V batteries with a capacity of 40, 60 and 80 Ah with a minimum number of 4000 charge cycles.

INDUSTRIAL COMPONENTS
The vehicle is built on standard industrial components that will ensure the availability and full compatibility of the part for many years. We try to use identical parts for individual models and thus ensure that all spare parts are in stock with us for delivery to the customer within 24 hours. Most of the components ensuring motion control, safety and AGV/AMR logic are made from Rockwell Automation products, a company that has long been a leader in the field of industrial automation.

EFFECTIVE WIRELESS CHARGING
Ensuring that the smooth operation of autonomous vehicles by recharging takes place while the activity is being performed (loading, unloading, waiting for instructions) so that the required cycle time, the production process, and the vehicle are not out of service due to recharging.
The high efficiency of battery use and minimisation of battery wear is ensured by contactless charging, which all our vehicles are equipped with and whose efficiency exceeds 90%. The chargers are intelligent and monitor the size of the charging current and the final voltage of the battery. Information about consumption and charging is also passed to the PLC. After charging the battery to the specified capacity, the charger is automatically disconnected.
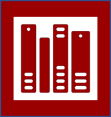
Master
For AGV/AMR, we offer different configurations of the MASTER switchboard with regard to the services required by the customer (Andon system – visualisation and monitoring, I/O control, remote supervision, connection with the customer’s technology) and concerning the number of autonomous vehicles required. MASTER gives commands to the vehicles, and they inform it back about their status. The system is adapted for the management of a fleet of vehicles and is compatible with the VDA5050 protocol.
Visualisation offers tools that help the customer with monitoring and predict potential maintenance and increase visibility of the current location and status of all AGV/AMRs in operation. It allows us to regularly back up all status reports and check the charging and discharging of the battery, the number of kilometres travelled and the progress of the current program in real-time. The complete visualisation can be accessed remotely not only on a PC but also on a mobile phone or tablet thanks to the integrated system Groove theme. This system also makes it possible to offer a clear and inexpensive ANDON system for large-scale equipment.
Remote monitoring enables connection to the MASTER switchboard at any time and from anywhere and promptly solves any problems or carries out SW adjustments to optimise the operation of autonomous vehicles
By controlling I/O, MASTER enables connection with existing systems at the point of AGV/AMR implementation and communication with these elements for smooth operation (control of gates, traffic lights, specification of loading and unloading points, etc.).
The MASTER switchboard enables communication and connection with other systems at the customer’s site (machines, lines, conveyors, etc.), which are necessary for the smooth and efficient operation of autonomous vehicles so that both technologies are aware of each other and work together (loading, unloading, stopping, starting, etc.).

TOUCH PANEL AND MULTIFUNCTION BUTTONS
Each of our AGVs/AMRs has a colour TFT panel of at least 4.3” to display more detailed information about the current status. It contains a set of control elements used for orientation in the menu of the panel and for controlling the vehicle itself. It displays alarm messages and battery statuses and enables the setting of some AGV user parameters. This panel can also be used with a tablet or mobile phone for monitoring. The panel is also extended by 5 mechanical buttons, and their position and function can be customised as required
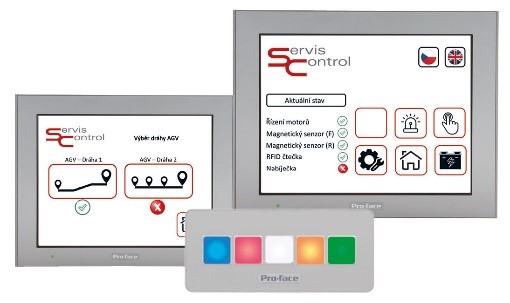